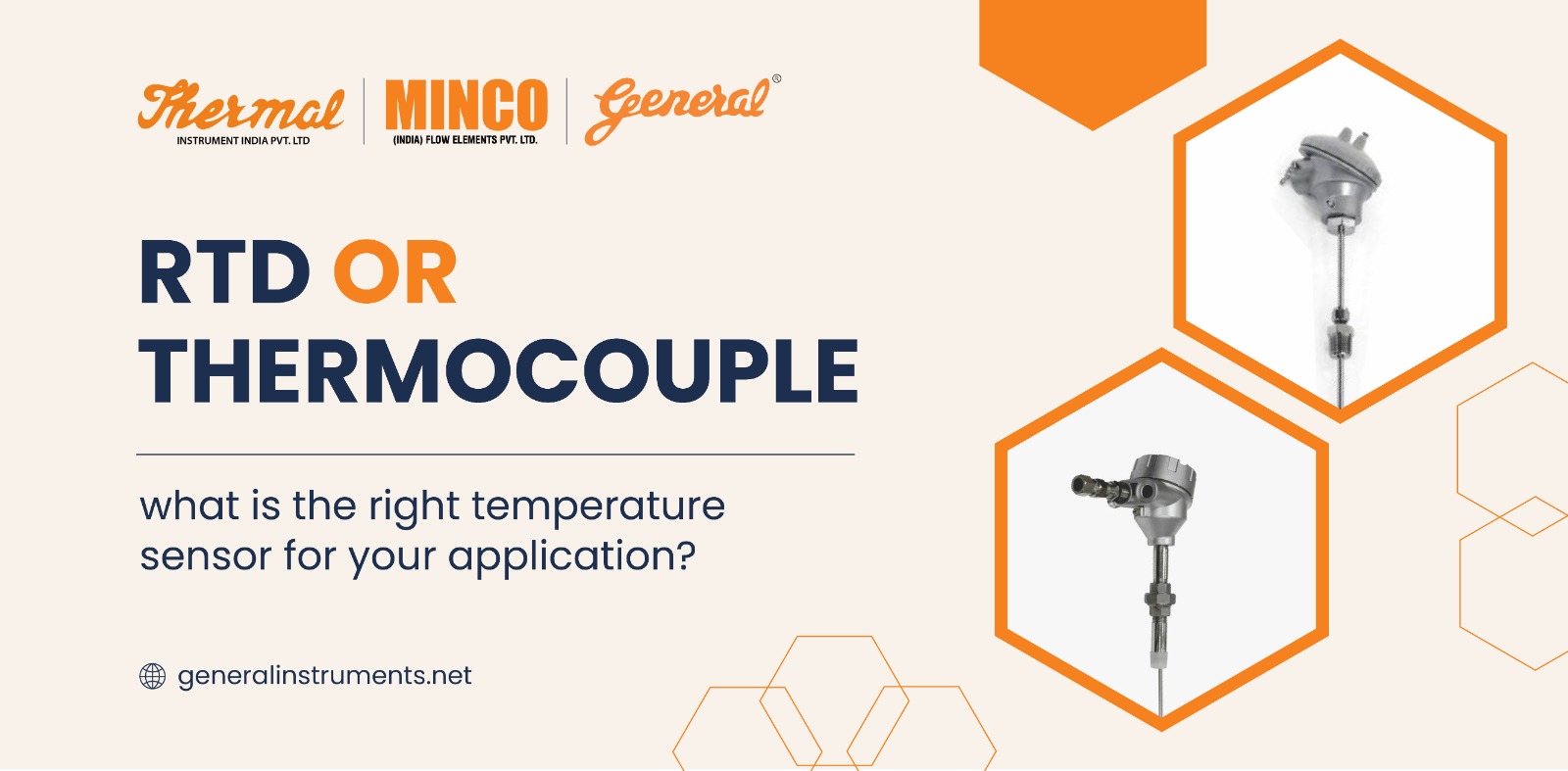
RTD or Thermocouple what is the right temperature sensor for your application?
Choosing the right temperature sensor for your industrial application can directly impact your process efficiency, product quality, and even safety. This blog delves into the two most common options: Resistance Temperature Detectors (RTDs) and thermocouples. It provides a clear and concise comparison to help you make an informed decision.
RTDs: Accuracy and Stability for Precise Measurements
RTD is like a skilled worker who always gets the job done correctly and consistently. It figures out the temperature by checking how much the electrical resistance in its measuring element changes. This means that it is very accurate (within ±0.5°C) and stays stable for a long time.
Strengths:
- Superior accuracy: Ideal for applications demanding tight temperature control.
- Excellent stability: Reliable long-term performance minimizes calibration needs.
- Linear output: Simplified signal conditioning and interpretation.
- Durable construction: Suitable for harsh industrial environments.
Weaknesses:
- Limited temperature range: Typically -200°C to +850°C.
- Slower response time: 1-2 seconds, not ideal for rapid fluctuations.
- Higher cost: Can be more expensive than thermocouples.
Thermocouples: Dynamic Versatility for Demanding Environments
Imagine an adventurous traveler who can adapt to any environment. A thermocouple is that. Based on the temperature differential between two different metals, it produces a voltage. Due to its extreme temperature tolerance (-250°C to +1800°C) and fast response time (milliseconds) to changes, it becomes extremely adaptable.
Strengths:
- Wide temperature range: Covers applications beyond RTD capabilities.
- Fast response time: Ideal for monitoring rapid temperature changes.
- Relatively low cost: Cost-effective option for many applications.
- Compact size: Suitable for tight spaces or intricate equipment.
Weaknesses:
- Lower accuracy: Typically, ±2°C, less precise than RTDs.
- Requires reference junction compensation: Adds complexity to signal conditioning.
- Susceptible to electrical noise: Needs proper shielding for accurate readings.
- Material degradation at high temperatures: May require regular replacement.
So, RTD or thermocouple? It depends on your specific application:
- Need high accuracy and long-term stability? Choose RTDs.
- Value fast response and wide temperature range? Thermocouples are your pick.
- Cost-sensitive application? Thermocouples might be sufficient.
- Harsh environment with rapid temperature changes? Consider thermocouples.
Beyond type, other factors influence your choice:
- Process pressure and temperature: Choose sensors rated for your specific conditions.
- Sensor immersion depth: Consider the sensor’s response time and accuracy as it relates to immersion depth.
- Power requirements: Some sensors require external excitation, impacting design and installation.
- Material compatibility: Ensure the sensor material won’t react with the measured medium.
Choosing the right temperature sensor is about finding the perfect balance between performance, cost, and practicality. Engaging with experienced professionals in process instrumentation can provide invaluable guidance to navigate the intricacies of RTDs and thermocouples, ensuring you select the sensor that perfectly aligns with your industrial needs.
Remember: There’s no one-size-fits-all solution. By understanding the strengths and weaknesses of RTDs and thermocouples alongside your specific application requirements, you can make an informed decision that optimizes your industrial process for the long term.