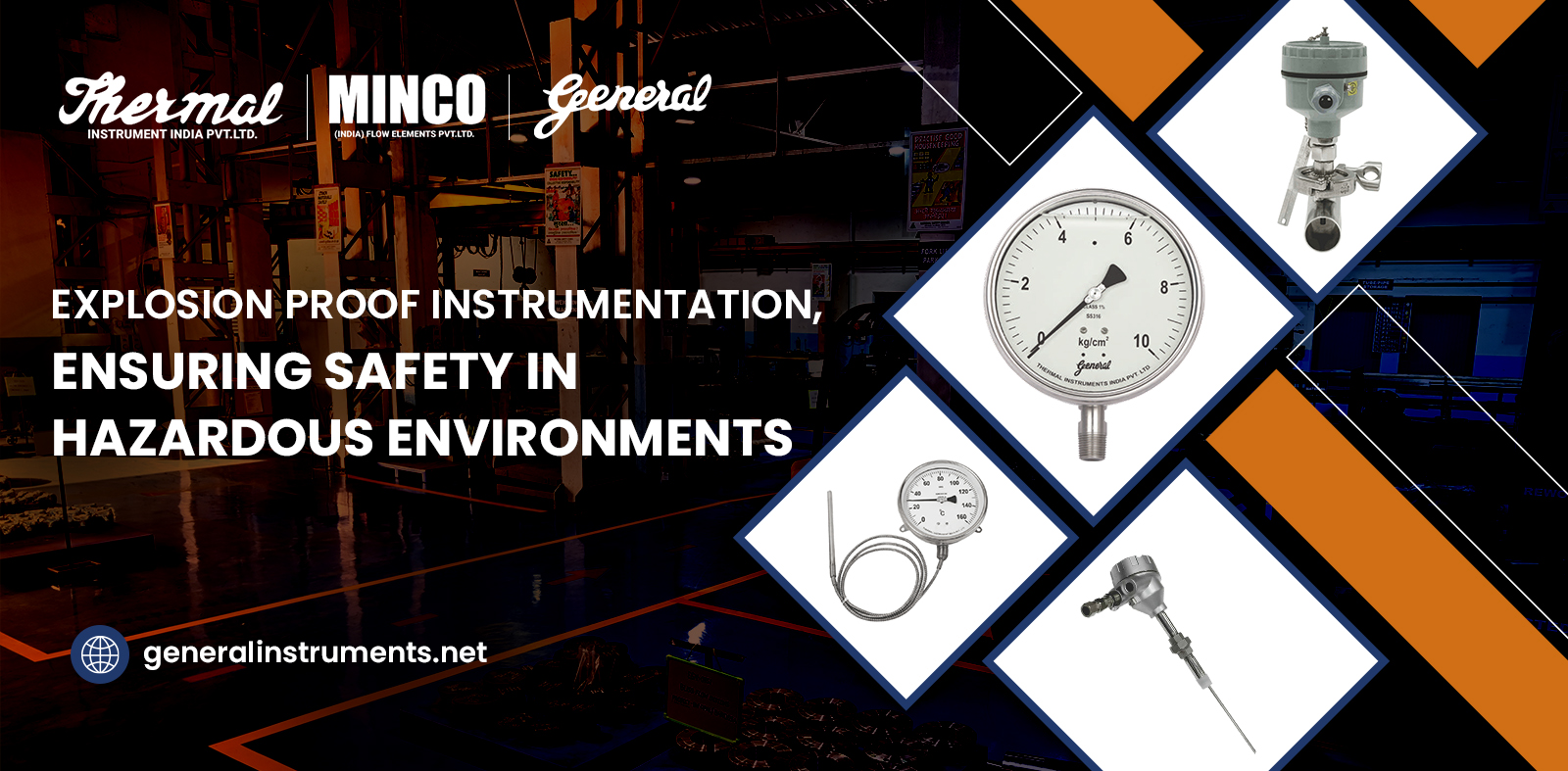
Explosion-Proof Instrumentation: Ensuring Safety in Hazardous Environments
In industries where explosive gases, vapours, or combustible dust are present, safety remains a top priority. Explosion-proof instrumentation is essential for maintaining secure and efficient operations in these hazardous areas. By designing devices that prevent ignition sources, explosion-proof equipment safeguards personnel, assets, and the surrounding environment, minimising the risk of catastrophic incidents.
What is Explosion-Proof Instrumentation?
Explosion-proof instrumentation is specifically engineered to operate safely in potentially explosive atmospheres. These devices are designed with rugged enclosures or housings that prevent internal sparks or heat from igniting external gases, dust, or vapours. They are extensively used in industries such as:
- Oil and Gas
- Chemical and Petrochemical Processing
- Mining
- Pharmaceuticals
- Food and Beverage
By containing any internal ignition within the instrument itself, explosion-proof equipment prevents hazardous atmospheres from causing combustion.
Why Explosion-Proof Instruments are Essential in Hazardous Areas
Industries dealing with flammable substances face significant operational risks, including fires, explosions, and toxic emissions. Explosion-proof instrumentation provides essential protection by preventing internal sparks, arcs, or hot surfaces from becoming ignition sources. Here’s why these instruments are indispensable:
- Safety Assurance: Protects employees, assets, and facilities from explosions or fires.
- Regulatory Compliance: Meets strict international safety standards such as ATEX, IECEx, and UL.
- Operational Continuity: Allows safe, continuous monitoring and control in hazardous conditions, reducing downtime.
Key Features of Explosion-Proof Instrumentation
Explosion-proof instruments are characterised by several key features that make them suitable for hazardous environments:
- Rugged Enclosures: Explosion-proof housings, typically constructed from materials like stainless steel or aluminium, contain any internal sparks or heat.
- Ingress Protection (IP) Ratings: High IP ratings (such as IP66 or IP67) ensure that the device is protected against dust and water ingress, further enhancing its durability.
- Certifications: Certified to meet international safety standards such as ATEX, IECEx, CSA, UL and PESO. These certifications specify the equipment’s capability to function safely in explosive atmospheres.
- Temperature and Pressure Ratings: Explosion-proof devices are rated to withstand extreme temperatures and pressures, ensuring reliability under adverse conditions.
- Customization: Often designed to meet specific environmental and operational needs, including resistance to chemicals, vibration, and other factors that could affect performance.
Types of Explosion-Proof Instrumentation
Explosion-proof instrumentation is available in a range of types and functionalities, including:
- Pressure Gauge: Provides accurate monitoring of pressure in explosive environments, critical for process control and safety.
- Temperature Gauge: Ensures reliable temperature measurement and monitoring in hazardous zones to maintain process integrity.
- Temperature Sensors: Enables precise temperature monitoring in explosive atmospheres.
Each type of instrument plays a role in monitoring and controlling specific processes within hazardous environments, contributing to both safety and operational efficiency.
Applications of Explosion-Proof Instrumentation
Explosion-proof devices are widely used across industries that handle flammable materials or operate in hazardous environments:
- Oil and Gas: Ensures safe monitoring of pressure, temperature, and flow in refineries, pipelines, and offshore drilling rigs.
- Chemical Processing: Prevents ignitions during chemical reactions and storage, where volatile substances are present.
- Mining: Protects against hazardous gases like methane in confined underground spaces.
- Food and Beverage: Ensures safe processing of flammable substances such as alcohol in beverage production.
- Pharmaceuticals: Monitors conditions in environments with combustible dust or volatile compounds.
Benefits of Using Explosion-Proof Instrumentation
Explosion-proof instrumentation not only enhances safety but also offers other benefits, including:
- Operational Efficiency: Allows continuous operations in hazardous areas, reducing costly shutdowns.
- Enhanced Durability: Built to withstand harsh conditions, resulting in a longer lifespan and reduced maintenance costs.
- Regulatory Compliance: Ensures that companies meet industry regulations, avoiding potential fines and shutdowns.
- Employee Safety: By preventing accidents, explosion-proof equipment protects workers and maintains a safe work environment.
Certifications and Standards: Ensuring Compliance in Hazardous Areas
Meeting regulatory standards is essential when working with explosion-proof instrumentation. Here are some common certifications and standards:
- ATEX (Atmosphères Explosibles): European standard ensuring equipment safety in explosive atmospheres.
- IECEx: International standard for safe equipment in explosive environments, often required globally.
- UL (Underwriters Laboratories): North American standard indicating compliance with safety and performance criteria.
- CSA (Canadian Standards Association): Canadian standard for safe operation in hazardous conditions.
- PESO (Petroleum and Explosives Safety Organization): Indian certification for hazardous areas.
By adhering to these certifications, companies can confidently operate in hazardous environments while ensuring regulatory compliance.
Choosing the Right Explosion-Proof Instrumentation
Selecting the appropriate explosion-proof equipment depends on several factors, including:
- Environmental Conditions: Consider temperature, pressure, humidity, and chemical exposure.
- Type of Hazard: Differentiate between gases, vapours, dust, and fibre hazards.
- Certification Requirements: Ensure the equipment meets necessary safety standards for the region of operation.
- Maintenance Needs: Opt for devices that require minimal maintenance to reduce downtime.
Conclusion: Investing in Safety with Explosion-Proof Instrumentation
In hazardous environments, explosion-proof instrumentation is a crucial investment in safety, efficiency, and compliance. By preventing potential ignition sources, this equipment protects workers, infrastructure, and surrounding communities from the dangers of explosions. At General Instruments Consortium (GIC), we provide reliable, certified explosion-proof instrumentation solutions tailored for demanding industrial environments.
Contact our experts today to learn more about our explosion-proof solutions and how we can help enhance safety in your operations.