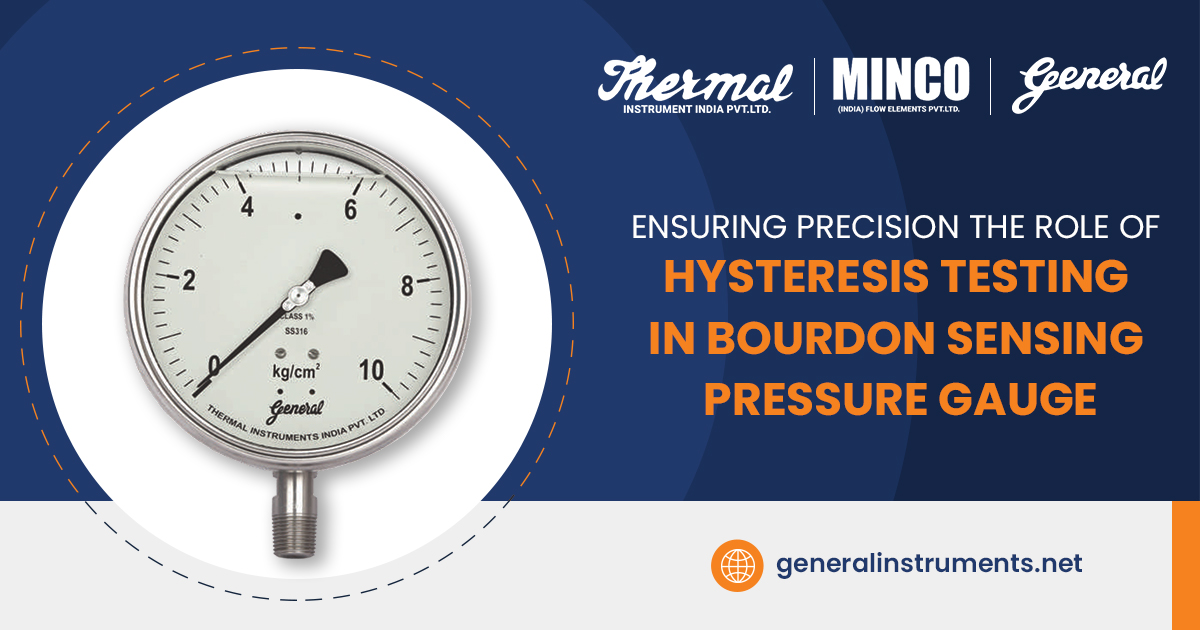
Ensuring Precision: The Role of Hysteresis Testing in Bourdon Sensing Pressure Gauge
At General Instruments Consortium, we pride ourselves on our commitment to reliability and innovation. Among the numerous products we offer, the Bourdon Sensing Pressure Gauge is a standout, renowned for its accuracy and durability. One of the critical aspects ensuring this precision is the rigorous process of hysteresis testing, among several other tests we conduct.
Understanding Bourdon Sensing Pressure Gauges
The Bourdon Sensing Pressure Gauge is a fundamental instrument used across various industries to measure pressure. Its mechanism is based on the Bourdon tube, a curved, hollow tube that deforms under pressure changes. As pressure increases, the tube straightens; as pressure decreases, the tube returns to its original shape. This deformation is translated into a dial reading, providing an accurate measurement of pressure.
The Importance of Hysteresis Testing
Hysteresis testing is one of the several vital tests we perform to ensure the accuracy and reliability of Bourdon Sensing Pressure Gauges. Hysteresis refers to the difference in the readings when pressure is applied and then removed. In an ideal scenario, a gauge should provide the same reading for a given pressure whether the pressure is increasing or decreasing. However, due to material properties and mechanical factors, there can be a slight variation, known as hysteresis error.
Steps in Hysteresis Testing
- Calibration: The gauge is first calibrated to ensure it is set to the correct standard.
- Pressure Application: Incremental pressure is applied to the gauge, and readings are taken at each step.
- Pressure Release: The pressure is then gradually released, and readings are taken again at each step.
- Comparison: The readings from the pressure application phase are compared to those from the pressure release phase to determine the hysteresis error.
Benefits of Hysteresis Testing
- Accuracy: By identifying and minimizing hysteresis errors, we ensure that our Bourdon Sensing Pressure Gauges provide precise readings.
- Reliability: Regular hysteresis testing helps in maintaining the long-term reliability of the gauges, ensuring they perform accurately over time.
- Customer Confidence: With rigorous testing protocols, customers can trust that instruments from the General Instruments Consortium will meet their stringent requirements for precision and reliability.
Conclusion
At the General Instruments Consortium, we are committed to upholding the highest standards of quality and precision in all our products. Our Bourdon Sensing Pressure Gauges undergo meticulous hysteresis testing, among other rigorous tests, to ensure they deliver accurate and reliable performance in every application. By investing in such comprehensive testing processes, we continue to reinforce our reputation as a trusted leader in the field of precision instrumentation.
For more information about our Bourdon Sensing Pressure Gauges, visit us today.